ALEX ESTRADA

SOLDADURA ELÉCTRICA
INDICE DE MATERIA DESARROLADA
PÁGINA
1. Definición de soldadura eléctrica 1
1.1 Principios fundamentales
1.2 Partes de un equipo
2. El electrodo, sus partes y el cebado 4
3. Descripción del trabajo realizado 6
4. Proceso de trabajo 8
5. Vistas de la pieza acotada 10
6. Hoja de pedido realizado para la práctica 11
7. Herramientas utilizadas 12
8. Seguridad e higiene 14
Anexo: Bibliografía
1. Definición de soldadura eléctrica
Se trata, en realidad, de distintos sistemas de soldadura, que tienen en común el uso de una fuente de alimentación eléctrica.
Ésta se usa para generar un arco voltaico entre un electrodo y el material base, que derrite los metales en el punto de la soldadura. Se puede usar tanto corriente continua (CC) como alterna (AC), e incluyen electrodos consumibles o no consumibles, los cuales se encuentran cubiertos por un material llamado revestimiento. A veces, la zona de la soldadura es protegida por un cierto tipo de gas inerte o semi inerte, conocido como gas de protección, y, en ocasiones, se usa un material de relleno.
Fuentes de energía
Para proveer la energía eléctrica necesaria para los procesos de la soldadura de arco, pueden ser usadas diferentes fuentes de alimentación. La clasificación más común de dichas fuentes consiste en separar las de corriente constante y las de voltaje constante. En la soldadura de arco, la longitud del arco está directamente relacionada con el voltaje, y la cantidad de calor generado está relacionada con la intensidad de la corriente. Las fuentes de alimentación de corriente constante son usadas con más frecuencia para los procesos manuales de soldadura tales como la soldadura de arco de gas con electrodo de tungsteno y la soldadura de arco metálico blindado, porque ellas mantienen una corriente constante incluso mientras el voltaje varía. Esto es importante en la soldadura manual, ya que puede ser difícil sostener el electrodo perfectamente estable, y como resultado, la longitud del arco y el voltaje tienden a fluctuar. Las fuentes de alimentación de voltaje constante mantienen éste y varían la corriente.
El tipo de corriente usado en la soldadura de arco también juega un papel importante. Los electrodos de proceso consumibles como los de la soldadura de arco de metal blindado y la soldadura de arco metálico con gas generalmente usan corriente directa (continua), por lo que el electrodo puede ser cargado positiva o negativamente, dependiendo de cómo se realicen las conexiones de los electrodos. En la soldadura, en caso de cargar el electrodo positivamente generará mayor de calor en el mismo, y como resultado, la soldadura resulta más superficial (al no fundirse casi el material base). Si el electrodo es cargado negativamente, el metal base estará más caliente, incrementando la penetración del aporte y la velocidad de la soldadura.
Sistema de soldadura
Uno de los tipos más comunes de soldadura de arco es la soldadura manual con electrodo revestido (SMAW, Shielded Metal Arc Welding), que también es conocida como soldadura manual de arco metálico (MMA) o soldadura de electrodo. La corriente eléctrica se usa para crear un arco entre el material base y la varilla de electrodo consumible, que es de acero y está cubierto con un fundente que protege el área de la soldadura contra la oxidación y la contaminación, por medio de la producción del gas CO2 durante el proceso de la soldadura. El núcleo en sí mismo del electrodo actúa como material de relleno, haciendo innecesario un material de relleno adicional.
El proceso es versátil y puede realizarse con un equipo relativamente barato, haciéndolo adecuado para trabajos domésticos y para trabajos de campo.Un operador puede hacerse razonablemente competente con una modesta cantidad de entrenamiento y puede alcanzar la maestría con la experiencia. Los tiempos de soldadura son algo lentos, puesto que los electrodos consumibles deben ser sustituidos con frecuencia y porque la escoria, el residuo del fundente, debe ser retirada después de soldar. Además, el proceso es generalmente limitado a materiales de soldadura ferrosos, aunque electrodos especializados han hecho posible la soldadura del hierro fundido, níquel, aluminio, cobre, acero inoxidable y de otros metales.
Video relacionado:
https://www.youtube.com/watch?v=VbIroqNEqto&list=PLBoygj3M5AZijq77iwWIk3r2LIUMdbhPp
1.1 Principios fundamentales
Calidad
Muy a menudo, la medida principal usada para juzgar la calidad de una soldadura es su fortaleza y la fortaleza del material alrededor de ella. Muchos factores distintos influyen en esto, incluyendo el método de soldadura, la cantidad y la concentración de la entrada de calor, el material base, el material de relleno, el material fundente, el diseño del empalme, y las interacciones entre todos estos factores. Para probar la calidad de una soldadura se usan tanto ensayos no destructivos como ensayos destructivos, para verificar que las soldaduras están libres de defectos, tienen niveles aceptables de tensiones y distorsión residuales, y tienen propiedades aceptables de zona afectada por el calor (HAZ). Existen códigos y especificaciones de soldadura para guiar a los soldadores en técnicas apropiadas de soldadura y en cómo juzgar la calidad éstas.
Geometría
Las soldaduras pueden ser preparadas geométricamente de muchas maneras diferentes. Los cinco tipos básicos de juntas de soldadura son la junta de extremo, la junta de regazo, la junta de esquina, la junta de borde, y la junta-T. Existen otras variaciones, como por ejemplo la preparación de juntas doble-V, caracterizadas por las dos piezas de material cada una que afilándose a un solo punto central en la mitad de su altura. La preparación de juntas solo-U y doble-U son también bastante comunes —en lugar de tener bordes rectos como la preparación de juntas solo-V y doble-V, ellas son curvadas, teniendo la forma de una U. Las juntas de regazo también son comúnmente más que dos piezas gruesas —dependiendo del proceso usado y del grosor del material, muchas piezas pueden ser soldadas juntas en una geometría de junta de regazo.


Soldabilidad
La calidad de una soldadura también depende de la combinación de los materiales usados para el material base y el material de relleno. No todos los metales son adecuados para la soldadura, y no todos los metales de relleno trabajan bien con materiales base aceptables. Hay que tener en cuenta el 60% del espesor base menor de las placas a unir para uso de uno de los catetos de la soldadura.
1.2 Partes de un equipo
Partes de Soldadores Eléctricos
Cuando usted adquiere un soldador eléctrico lo que busca, básicamente, es que sea de utilidad para la actividad a realizar, aunque el usuario, en general, no tiene mayor conocimiento sobre las partes que lo constituyen. Los especialistas o profesionales que tienen experiencia en ello, lo primero que se preguntan es qué partes constituyen el soldador y qué beneficios les traerá esta máquina.
Aquí encontrará información sobre algunas de las partes con las que cuentan los soldadores eléctricos, en su gran mayoría. Hay que tener en cuenta que las operaciones que se realizan con esta herramienta pueden llegar a ser peligrosas, por lo cual es necesario tomar las medidas de seguridad correspondientes y utilizar el soldador que corresponda
Partes de un Soldador Eléctrico
-
Máquina de Soldar. Es la parte más importante dentro del soldador. Es un conjunto de elementos que proporcionan la energía para realizar el trabajo.
-
Cable de Tierra o Neutro. Cable que va conectado a la pieza donde encontramos al electrodo.
-
Cable Porta Electrodo. Cable que sale del bobinado, hacia la pieza.
-
Porta Electrodo. Donde se ubica el electrodo que utilizaremos para soldar.
-
Varilla de Soldadura o Electrodo. Es la varilla que realiza la soldadura.
-
Cable Para Conectar a la Toma de Corriente. El cable de conexión eléctrica, para que pueda funcionar el soldador eléctrico.
-
Manija Para Regulación de Amperaje. Se utiliza para regular el amperaje que se requiera, según las características del trabajo que se vaya a realizar.
-
Botón de Apagado y Encendido. Es el switch con cual se enciende y apaga el paso de corriente.
-
Switch de Alto o Bajo Voltaje. El botón para habilitar la regulación del voltaje y poder graduarlo con la manija.
-
Bornes de Conexión de Cables de Tierra y Cable Porta Electrodo. Es un cable que une el bobinado con la pieza.
-
Seguro de la Soldadora Eléctrica. Es la parte que sirve para asegurar el electrodo y se pueda dar de mejor manera la soldadura.

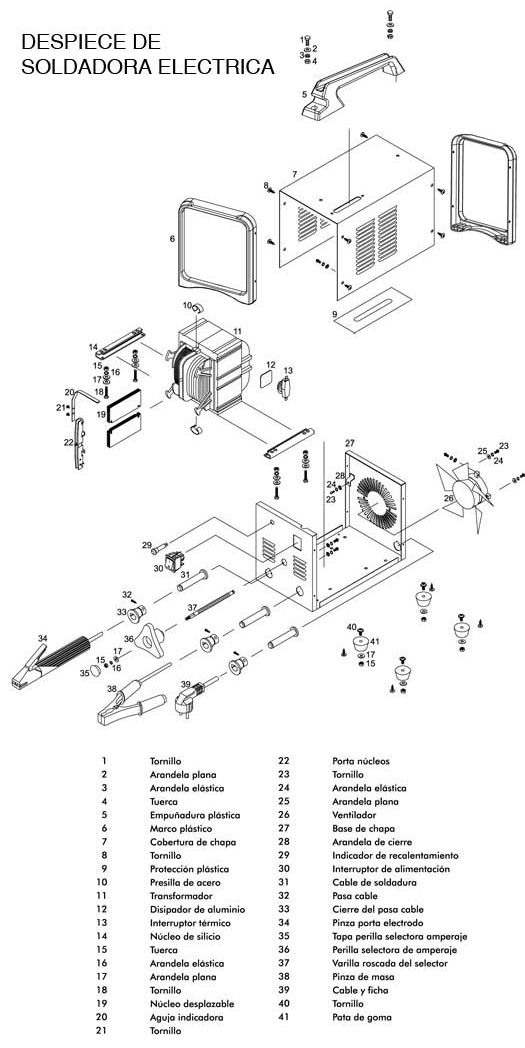
2. El electrodo, sus partes y el cebado
En la soldadura por arco se emplea un electrodo como polo del circuito y en su extremo se genera el arco eléctrico. En algunos casos, también sirve como material fundente. El electrodo o varilla metálica suele ir recubierta por una combinación de materiales diferentes según el empleo del mismo. Las funciones de los recubrimientos pueden ser: eléctrica para conseguir una buena ionización, física para facilitar una buena formación del cordón de soldadura y metalúrgica para conseguir propiedades contra la oxidación y otras características.
PARTES DE UN ELECTRODO
Los Electrodos Metalicos Revestidos se componen de dos partes:
· Núcleo y
· Revestimiento
FUNCION DEL NUCLEO
El núcleo cumple dos funciones muy importantes a saber: Conducir la Electricidad y Aportar Material Relleno.
FUNCIONES DEL REVESTIMIENTO
El revestimiento como tal tiene varias funciones en el proceso SMAW. El 90% del trabajo lo ejerce el revestimiento y estas funciones son a saber:
1. FUNCION MECANICA
2. FUNCION ELECTRICA
3. FUNCION METALURGICA
4. FUNCION PROTECTORA
5. FUNCION TERMICA
· FUNCION ELECTRICA
Esta funcion permite mantener el Arco y se logra a traves del dioxido de titanio.
· FUNCION MECANICA
Esta funcion es la encargada de guiar el arco en una determinada direccion concentrandolo sobre la junta, ademas favorece la buena penetración del cordon de soldadura en el metal base.
El revestimiento cumple con una condicion de velocidad de fusion mas tardia que la del núcleo, a fin de que se forme un crater en el extremo del electrodo de longitud adecuada , evitando axial que el elctrodose pegue al material base cuando estamos soldando.
· FUNCION METALURGICA
Esta funcion la cumple la escoria, afinando el cordon de soldadura , mejorando las propiedades mecanicas del metal depositado con una energica accion depuradora, limpiando el charco fundido de las impurezas tales como: Fosforo ( P ) y Azufre ( S ).
· FUNCION PROTECTORA
Esta funcion cumple la propiedad de proteger el baño o charco de metal fundido contra los ajentes contaminantes del aire tales como el Oxigeno ( O2 ) y el nitrogeno ( N2 ), durante el proceso que sufre el metal fundido del estado liquido, pastoso a solido, cuando esta fundiendo el electrodo y la pieza a soldar. Esta funcion la ejerce el Carbonato de Calcio.
· FUNCION TERMICA
Esta funcion tambien la ejerce la escoria ya que es la encargada de retardar el enfriamiento del metal depositado dando asi un tratamiento termico correcto al cordon de soldadura.
Estas funciones facilitan el encendido y estabilizan el arco, reemplazan ciertos elementos del metal de aporte, que se volatilizan, debido a las altas temperaturas del arco. Permiten el empleo de corriente alterna y continua. Ayudan al control de la penetración balanceando la energia del arco. Mejoran las propiedades de la zona de fusión, proveen elementos desoxidantes y desulfurantes, aportan elementos de aleación adicionales tales como: Cr, Mn, Ni.


EL CEBADO
Proceso por el cual se calienta el electrodo sobre una masa de sufrimiento. De esta forma se evita que el electrodo se pegue a la pieza a soldar al iniciar la soldadura por arco.
Es una parte muy importante en este trabajo, sobretodo para los profesionales mas inexpertos.

3. Descripción del trabajo a realizar
En esta práctica vamos a practicar la soldadura por arco. Para ello utilizaremos material en chapas de acero.
Lo primero que aprenderemos son las partes de un equipo de soldadura eléctrica y como funciona. También nos mostarán todas las herramientas a utilizar y el sistema de aspiración de seguridad para los gases desprendidos durante el trabajo.
Durante el aprendizaje
Utilizaremos chapas de acero de 1,5 milimetros de espesor cortadas mediante prensa cortadora.
En estas chapas prácticaremos a "echar cordones" rectos y de grosor constante y suficiente.
En la segunda parte de la práctica, con los mismos materiales, aprenderemos a unir dos chapas con un solo cordón de soldadura.
Durante el examen
Primera parte
Tras los reiterados intentos y práctica de los cordones, mostraremos nuestro trabajo a los profesores de la asignatura.De esta forma podrán comprobar nuestra progresión y el nivel que hemos alcanzado.
Tendremos la oportunidad de un último intento y definitivo para conseguir la nota deseada.
Segunda parte
Una vez aprobada y superada la primera parte de la práctica, procederemos a la segunda con los mismos materiales utilizados en la primera.
Esta parte del examen es mas complicada y requiere de un buen proceso de unión por puntos entre las dos chapas a unir.


4. Proceso de trabajo
Como ya se ha descrito en el apartado anterior se va a realizar una práctica de soldadura por arco eléctrico.
Primera parte
1. Empezamos la práctica con el trazado de unas lineas horizontales con tiza sobre las chapas de 1,5 mm de espesor. Estas lineas nos permitiran realizar los cordones de forma recta.
2. A continuación conectamos la máquina eléctrica y la regulamos a la intensidad deseada.
3. Colocamos la masa en la mesa y un electrodo en la pinza.
4. Nos colocamos la mascara pantalla protectora.
5. Cebamos el electrodo.
6. Echamos el cordón sobre la chapa.
7. Cogemos la chapa con unos alicates y nos la llevamos al banco de trabajo fuera de la cabina de soldadura.
8. Con una piqueta y un cepillo de puas de acero, descascarillamos la soldaura.
Segunda parte
1. Elegimos las dos chapas que vamos a unir.
2. A continuación conectamos la máquina eléctrica y la regulamos a la intensidad deseada.
3. Colocamos la masa en la mesa y un electrodo en la pinza.
4. Nos colocamos la mascara pantalla protectora.
5. Cebamos el electrodo.
6. Ponemos 3 puntos de soldadura entre las dos chapas. 1 al inicio y al final de la unión y otro en medio.
7. Echamos el cordón sobre la chapa.
8. Cogemos la chapa con unos alicates y nos la llevamos al banco de trabajo fuera de la cabina de soldadura.
9. Con una piqueta y un cepillo de puas de acero, descascarillamos la soldaura.

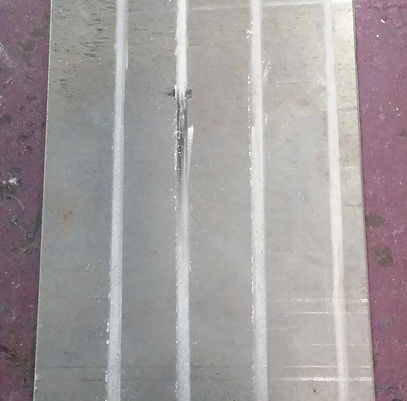
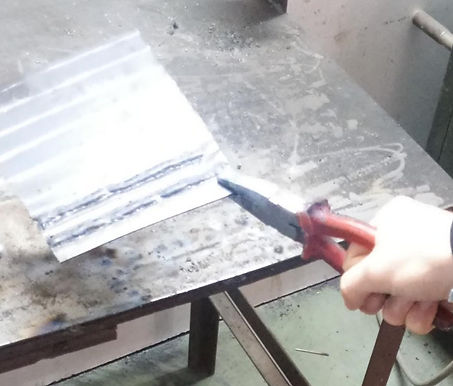

5. Vistas de la pieza acotada


6. Hoja de pedido de material
Para la realización de la práctica vamos a necesitar:
- chapas de acero de 1,5 milimetros de espesor
- 1 tiza
- 1 regla
- 10 o 15 electrodos de 2,5 milimetros
7. Herramientas
A continuación se muestra una relación de las herramientas utilizadas en imagenes:


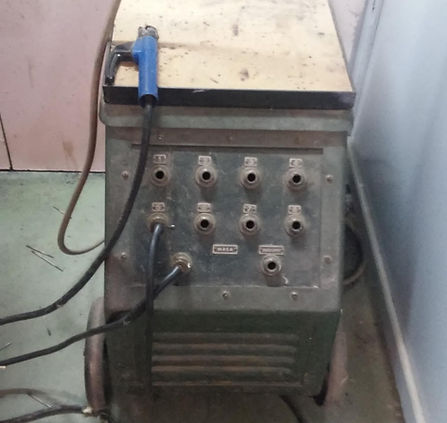
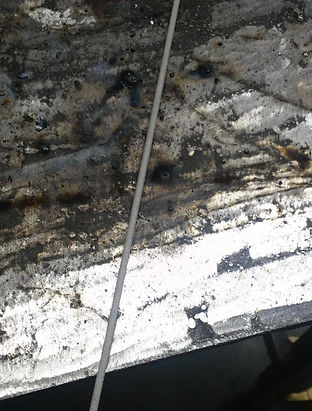
8. Seguridad e higiene
Los riesgos principales por soldadura por capilaridad son:
- Altas temperaturas asociadas al arco eléctrico y los materiales fundidos que se producen, tanto formando la soldadura como
proyecciones que se desprenden de la misma, del equipo que se utiliza para la soldadura.
- Toxicidad de los gases combustibles que se usan y de los vapores de consumibles y materiales base que se funden y/o calientan
- Nivel de ruidos producidos no quizá durante la soldadura sino durante procesos asociados a la ejecución de la misma, como uso
de radiales para desbarbado, corte, limpieza .
- Radiaciones luminosas procedentes de la llama y de los metales incandescentes.
Como medidas de protección utilizaremos EPIS y colectivas:
- Guantes para evitar quemaduras por contacto o por impacto directo
- Ropa protectora
- Detector de humos que señalen cuando hay acumulación abuntante de gases
- Buena ventilación para evitar la acumulación de humos
- Lugar de trabajo limpio y seguro
- Mandil
- Careta o mascarrilla protectora antimpactos
- Careta o mascarilla protectora de radiación luminica
A continuación veremos una series de EPIS y medidas colectivas

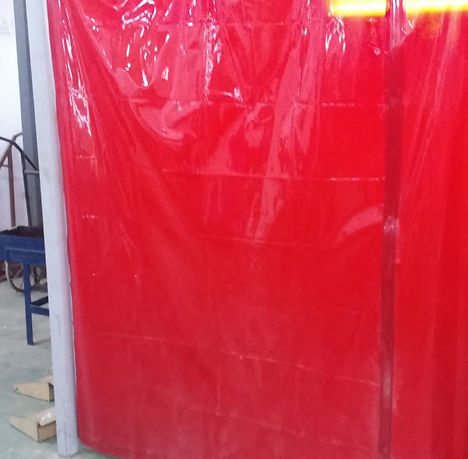
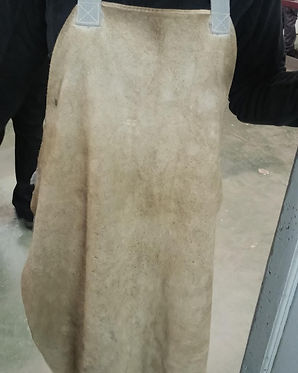
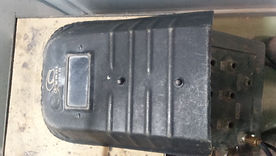

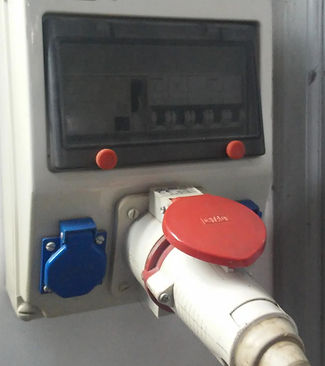


Anexo: Bibliografía
Fotos tomadas durante las prácticas en taller
Apuntes de clase de 1º EEEST, Virgen de los Reyes
http://solysol.com.es/data/documents/Seguridad=20e=20Higiene=20Soldadura.pdf
http://www.cebora.it/istr/ist190E.pdf
https://es.wikipedia.org/wiki/Soldadura_el%C3%A9ctrica
http://es.wikihow.com/soldar-con-arco-el%C3%A9ctrico
Video relacionados con la práctica:
https://www.youtube.com/watch?v=Y6zzw_FM0Vg
https://www.youtube.com/watch?v=8CFFXkqpnPg
Tutorial de Ramon Recuero Ibañez:
https://www.youtube.com/watch?v=VbIroqNEqto&list=PLBoygj3M5AZijq77iwWIk3r2LIUMdbhPp