ALEX ESTRADA

PRÁCTICA UPN
INDICE
1. Define que es el acero. Tipos de aceros aleados
2. Tratamientos térmicos del acero
3. Define corrosión y oxidación. Tratamientos para evitarlas
4. Proceso de trabajo
5. Croquis acotado de la pieza original y finalizada
6. Hoja con la petición de los materiales y herramientas
7. Seguridad e higiene
8. Bibliografía
1. Define que es el acero
El acero: químicamente es una aleación de hierro y carbono (c=0.05% hasta menos de 2%), aparte de otros metales y metalaloides que coexisten en forma de solución sólida (<1,65% de manganeso, el 0,60% de silicio y el 0,60% de cobre).
Se denomina acero a aquellos productos ferrosos cuyo porcentaje de carbono está comprendido entre 0,05 y 1,7 %.
El acero es uno de los materiales de fabricación y construcción más versátil y adaptable. Ampliamente usado y a un precio relativamente bajo, el acero combina la resistencia y la trabajabilidad, lo que se presta a fabricaciones diversas. Asimismo sus propiedades pueden ser manejadas de acuerdo a las necesidades específicas mediante tratamientos con calor, trabajo mecánico, o mediante aleaciones.
El Acero funde entre 1400 y 1500ºC pudiéndose moldear más fácilmente que el hierro.
Resulta más resistente que el hierro pero es más propenso a la corrosión. Posee la cualidad de ser maleable, mientras que el hierro es rígido.
La ecuación de la reacción química fundamental de un alto horno es:
Fe2O3 + 3 CO => 3 CO2 + 2 Fe
Acero de baja aleación y alta aleación. 4% peso de los aleantes.
Video de fabricación del acero
1.1 Tipos de aceros aleados
Estos aceros contienen una proporción determinada de vanadio, molibdeno y otros elementos, además de cantidades mayores de manganeso, silicio y cobre que los aceros al carbono normales.
Acero aleado es una posible variedad de elementos químicos en cantidades en peso del 1,0 % al 50 % para mejorar sus propiedades mecánicas. Los aceros aleados se dividen en dos grupos: aceros de baja aleación y aceros de alta aleación. La distinción entre los dos varía: Smith and Hashemi sitúan la barrera en el 4 % en peso de aleantes, mientras que Degarmo lo define en el 8,0 %.1 2 La expresión acero aleado designa más comúnmente los de baja aleación.
Todo acero es en realidad una aleación, pero no todos los aceros son "aceros aleados".
Los aceros más simples son hierro (Fe) (alrededor del 99 %) aleado con carbono (C) (alrededor del 0,1 -1 %, dependiendo del tipo). Sin embargo, el término "acero aleado" es el término estándar referido a aceros con otros elementos aleantes además del carbono, que típicamente son el manganeso (el más común), níquel, cromo, molibdeno, vanadio, silicio, y boro. Aleantes menos comunes pueden ser el aluminio, cobalto, cobre, cerio, niobio, titanio, tungsteno, estaño, zinc, plomo, y zirconio.
La mejora de propiedades de los aceros aleados se muestra a continuación, con respecto a los aceros al carbono: resistencia, dureza, tenacidad, resistencia al desgaste, templabilidad, y resistencia en caliente.
Para alcanzar esas mejores propiedades el acero puede necesitar un tratamiento térmico.
Algunos de estos aceros aleados encuentran aplicaciones altamente exigentes, como en los álabes de turbina de un motor de reacción, en vehículos espaciales, y en reactores nucleares. Debido a las propiedades ferromagnéticas del hierro, algunos aceros aleados tiene aplicaciones en donde su respuesta al magnetismo es muy importante, como puede ser un motor eléctrico o un transformador.
Aceros de baja aleación
Se emplean estos aceros para alcanzar una templabilidad mayor, lo cual mejora otras propiedades mecánicas. También se usan para aumentar la resistencia a la corrosión en ciertas condiciones ambientales.
Los aceros de baja aleación con contenidos medios o altos en carbono son difíciles de soldar. Bajar el contenido en carbono hasta un 0,10 % o 0,30 %, acompañada de una reducción en elementos aleantes, incrementa la soldabilidad y formabilidad del acero manteniendo su resistencia. Dicho metal se clasifica como un HSLA Steel (acero de baja aleación de alta resistencia).
Algunos aceros de baja aleación comunes son:
-
D6AC
-
300M
-
256A
1.2 Clasificación de los aceros aleados de acuerdo con su utilización
Aceros aleados: Contienen, además del carbono otros elementos en cantidades suficientes como para alterar sus propiedades. Pueden ser de baja o alta aleación.
Uso: estructuras, herramientas, engranajes, etc.
Los elementos que se añaden principalmente son:
Carbono: Aumenta la dureza y fragilidad. Mayor resistencia al desgaste.
Cromo y níquel: aumenta la resistencia a la corrosión (Aceros inoxidables)
Manganeso: mejora la soldabilidad
Vanadio: mejora la dureza
A continuación se señalan los grupos clásicos:
a) Aceros en los que tiene una importancia fundamental la templabilidad
Aceros de gran resistencia
Aceros de cementación
Aceros de muelles
Aceros indeformables
b) Aceros de construcción:
Aceros de gran resistencia
Aceros de cementación
Aceros para muelles
Aceros de nitruración
Aceros resistentes al desgaste
Aceros para imanes
Aceros para chapa magnética
Aceros inoxidables y resistentes al calor
c) Aceros de herramientas:
Aceros rápidos
Aceros de corte no rápidos
Aceros indeformables
Aceros resistentes al desgaste
Aceros para trabajos de choque
Aceros inoxidables y resistentes al calor.
2. Tratamientos térmicos del acero
Consisten en calentar el acero y enfriarlo después, para modificar la microestructura (tamaño de grano), homogeneidad final y con ello se cambia la resistencia, ductilidad, etc.
Estas transformaciones dependen fundamentalmente de la temperatura alcanzada y la velocidad de enfriamiento.
Tipos de tratamiento:
-
Recocido
-
Normalizado
-
Temple
-
Revenido
-
otros tratamientos: temple superficial, cementación, cianuración, nitruración ...
-
Recocido:
-
se calienta (> Tª crítica) y se enfría muy lentamente (horno)
-
se consigue afinar el grano y la forma de los cristales
-
ablanda el acero, elimina las tensiones de laminación y aumenta la ductilidad
-
-
Normalizado:
-
se calienta (> Tª crítica) y se enfría al aire libre
-
se utiliza para eliminar las tensiones internas
-
-
Temple:
-
se calienta (> Tª crítica) y se enfría rápidamente (en agua)
-
aumenta el límite elástico, carga de rotura y dureza
-
en cambio baja el alargamiento, fragiliza la estructura del acero teniendo menos tenacidad y ductilidad
-
se obtiene martensita
-
-
Revenido:
-
se calienta (< Tª crítica) y se enfría lentamente (al aire)
-
se aplica tras el temple para disminuir la fragilidad
-
Video de tratamientos térmicos
5. Otros tratamientos
Consisten en introducir en la superficie del acero ciertos elementos químicos, modificando la composición.
Cementación
Aumento de la cantidad de C superficial, aumentado la dureza, puede hacerse con medios sólidos, líquidos o gaseosos. Utilizando carbonatos o CO, la superficie de 0.5 a 3.5 mm. Exterior diferente al interior.
Nitruración
Cementación con nitrógeno, formando nitruros alojados en los intersticios.
Cianuración
Saturación con C y N, baño de cianuro sódico y carbonato sódico (770-870ºC)
3. Define corrosión y oxidación. Tratamientos para evitarlas.
Los materiales están expuestos continuamente a los más diversos ambientes de interacción material-ambiente provoca, en muchos casos, la pérdida o deterioro de las propiedades físicas del material. Los mecanismos de deterioro son diferentes según se trate de materiales metálicos, cerámicos o polímeros (plásticos). Así, en el hierro, en presencia de la humedad y del aire, se transforma en óxido, y si el ataque continúa acaba destruyéndose del todo. Desde el punto de vista económico, la corrosión ocasiona pérdidas muy elevadas.
En los materiales metálicos, el proceso de deterioro se llama oxidación y corrosión. Por otro lado, en los cerámicos las condiciones para el deterioro han de ser extremas, y hablaremos también de corrosión. Sin embargo, la pérdida de las propiedades de los materiales polímeros se denomina degradación.
Video de oxidación y corrosión
En el deterioro de materiales podemos distinguir dos procesos:
-
Oxidación directa.
Resulta de la combinación de los átomos metálicos con los de la sustancia agresiva. Ejemplos:
2 Fe + O2 → 2 FeO (herrumbre-óxido) (oxidación por oxígeno como causa).
En este caso, los productos de la reacción quedan adheridos a la superficie del metal. En algunos casos, se forman películas protectoras que los aíslan del agente corrosivo. El caso más corriente es el ataque por oxígeno. En este caso, sobre el metal se forma una capa de óxido que, en algunos casos autoprotege al metal de una mayor oxidación. Cu, Ni, Sn, Al, Cr,... Los ambientes son secos.
Pero el oxígeno no es el único agente, pues también puede intervenir el cloro (Cl2), el azufre (S), el hidrógeno (H2), el monóxido de carbono (CO), el dióxido de carbono (CO2),...
Fe + S → FeS (sulfuro) (oxidación por azufre como causa)
Esto lleva a que el metal, con el tiempo, pase de tener un estado libre (puro) a tener un estado combinado con otros elementos (óxidos, carbonatos, sulfatos,...)
En los procesos de oxidación, los metales pasan de su estado elemental a formar iones positivos (cationes) por pérdida de electrones.
M → M++ ne-
siendo n el número de electrones que se pierden.
A esta reacción se le llama reacción de oxidación o reacción anódica. El proceso de oxidación se acelera si la temperatura de eleva.
2. Corrosión electroquímica o corrosión en líquidos.
En este caso, el metal es atacado por un agente corrosivo en presencia de un electrolito. (Un electrólito o electrolito es cualquier sustancia, normalmente líquida, que contiene iones libres, que se comportan como un medio conductor eléctrico.
Normalmente un electrolito es una disolución, en la que el disolvente suele ser agua y el soluto otra sustancia). El ejemplo más conocido es el agua del mar (el cloruro sódico es un agente corrosivo), que actúa como electrolito.
Los procesos de corrosión son procesos electroquímicos, ya que en la superficie del metal se generan “micropilas galvánicas” en las que la humedad actúa como electrolito. El metal actúa como ánodo (polo positivo) y, por lo tanto, se disuelve. Así, el electrolito actúa como medio conductor a través del cual viajan las cargas que abandonan los electrones del ánodo que se corroe, el metal.
Existe un tipo de corrosión de tipo electroquímico que aparece cuando se juntan metales diferentes o son conectados eléctricamente. Al producirse el contacto, el metal más electronegativo desempeña el papel de ánodo y, por tanto, sufre la corrosión.
Definiciones que nos aclaran las cosas:
-
Ánodo: Metal que cede electrones y se corroe.
-
Cátodo: Receptor de electrones.
-
Electrolito: Líquido que está en contacto con el ánodo y el cátodo. Debe ser conductor eléctrico. Este líquido proporciona el medio a través del cual se asegura el desplazamiento de cargas eléctricas desde el ánodo hasta el cátodo.
3.1. Protección contra la oxidación y la corrosión
Impedir la corrosión implica impedir reacciones electroquímicas. Es decir, eliminar la posible presencia de un electrolito que actúe como medio conductor para facilitar una reacción de transferencia de electrones desde un metal anódico. Así, las soluciones podrían ser:
a) Protección por recubrimiento. Es decir, crear una capa o barrera que aísle el metal del entorno. Dentro de este tipo de protección podemos hallar:
1. Recubrimientos no metálicos: siendo los más comunes...
- Pinturas y barnices: Es económico y exige que la superficie esté limpia de óxidos y grasas
- Plásticos: Son muy resistentes a la oxidación y son flexibles, pero apenas resisten el calor. El más empleado es el PVC.
- Esmaltes y cerámicos: Tiene la ventaja de resistir las altas temperaturas y los desgastes.
2. Recubrimientos metálicos.
- Inmersión: Se recubre el metal a proteger en un baño de metal fundido. El metal al solidificar forma una fina capa protectora. Los metales más empleados son...
Estaño (la técnica se llama estañado): latas de conserva
Aluminio (la técnica se llama aluminización): Es económico y con calidad.
Plomo (la técnica se llama plombeado): Para recubrir cables y tuberías.
Cinc (la técnica se llama galvanizado): Para vigas, vallas, tornillos,... y otros objetos de acero.
- Electrodeposición. En este caso se hace pasar corriente eléctrica entre dos metales diferentes que están inmersos en un líquido conductor que hace de electrolito. Uno de los metales será aquel que hará de ánodo, el cual se oxidará y sacrificará. El otro metal, el que se desea proteger, hará de cátodo y ambos estarán inmersos en el electrolito que estarán en una cuba. Cuando pasa la corriente eléctrica, sobre el metal catódico se crea una fina capa protectora hecha del material procedente del metal anódico, pues la pila obliga a ceder electrones al ánodo que alcanzarán al cátodo. Cuando el metal que hace de cátodo y se desea proteger es acero y el otro que va a protegerlo (que hace de ánodo) es cinc, el proceso se llama galvanizado.
- Protección por capa química: Se provoca la reacción de las piezas con un agente químico que forme compuestos en su superficie que darán lugar a una capa protectora. Por ejemplo:
Cromatizado: Se aplica una solución de ácido crómico sobre el metal a proteger. Se forma una capa de óxido de cromo que impide su corrosión.
Fosfatación: Se aplica una solución de ácido fosfórico y fosfatos sobre el metal. Se forma una capa de fosfatos metálicos que la protegen del entorno.
- Inhibidores: Se trata de añadir productos químicos al electrolito para disminuir la velocidad de la corrosión. Ejemplo: Sales de cromo. Se echan a los radiadores de los coches.
4. Proceso de trabajo
En este apartado vamos a describir los pasos que hemos dado en el taller para la obtención, trabajo y resultado final sobre nuestra pieza.
Antes de entrar en el trabajo que hemos realizado durante el primer trimestre en la práctica del perfil metálico, es importante destacar como los profesores nos enseñaron el taller, lugar donde hemos realizado toda la práctica. Fuimos en grupo toda la clase María José y Flores nos mostraron todos los armarios y herramientas del taller para que nos fuéramos familiarizándonos.
La práctica consistía en darle unas medidas y características finales a una pieza de viga de acero en forma de U. Debíamos reducirle las alas 5 milímetros, conseguir que todas sus caras llegaran a escuadra y a nivel, eliminar la curva entre el alma y las alas de pieza haciendo que estas estuvieran perpendiculares y por último realizar 3 taladros y darle roscas a cada uno de ellos en el alma.
Paso 1. Obtención de la pieza
El primer día de taller los profesores nos dieron a cada alumno la pieza con la que íbamos a trabajar individualmente. Esta pieza fue obtenida mediante el corte de un perfil UPN 80 en partes más pequeñas. Vistas 1
Paso 2. Medida de la pieza
Con la pieza ya en la mano y con la ayuda de un pie de rey, obtuvimos las medidas de nuestra U. Estas medidas fueron plasmadas en un croquis que hicimos en ese mismo momento en un formato A4.
Paso 3. Sujeción de la pieza al banco de trabajo
Para poder trabajar sobre la U con facilidad y para que no se nos moviera, utilizamos un tornillo fijo. Estos tornillos están anclados a los bancos o mesas de trabajo que hay en el taller. Colocamos la pieza los más horizontal posible y con las alas hacia arriba, de este modo podemos empezar a limarlas para llegar hasta la medida deseada.
Paso 4. Limado de las alas
Utilizamos una lima plana de gran tamaño siguiendo el método aprendido en las clases teóricas dadas por la profesora María José. Era importante limar cada ala por separado y teniendo muy presente el intentar usar la lima lo más horizontal posible. Durante este paso tuvimos que medir reiteradas veces nuestra pieza para asegurarnos de que llegásemos a la medida necesaria. Foto 1, foto 2 y foto 3
Paso 5. Perpendicularidad entre las alas y el alma.
En este paso se trataba de conseguir que las alas y el alma de nuestra U formaran un ángulo de 90º, el cual podríamos comprobar con una pequeña escuadra de metal que nos fue facilitada por los profesores.
Para ello utilizamos en primer lugar una lima triangular que nos ayudó a eliminar la parte curva de la pieza.
Después de conseguir un firme liso para el limado procedimos, mediante una lima plana de tamaño medio, al limado de las alas para conseguir la perpendicularidad entre el alma y las alas. Durante este proceso fuimos comprobando con la escuadra que no reducíamos el perfil por un lado más que por otro. Foto 4
Paso 6. Perpendicularidad de las caras.
Debido al corte inicial para la obtención de la pieza, las caras de esta no se quedaron muy lisas. Para corregir este error, volvimos a colocar la pieza en el tornillo de forma vertical.
Una vez colocada la pieza y lista para poder trabajar sobre ella, utilizamos la misma lima plana de gran tamaño que la del paso 3. De nuevo con la ayuda de la pequeña escuadra conseguimos el resultado deseado. Vistas 3 e isometría 3
Paso 7. Limpiado y alisado de todas las caras.
Con la inigualable ayuda del tornillo, procedimos a limar cada una de las caras de nuestra pieza con el único fin de eliminar la primera capa de suciedad que tenía. Para ello utilizamos una lima plana pero teniendo en cuenta que debíamos retirar la misma cantidad de material en toda su superficie, evitando así resaltos en sus caras. Con esto llegamos a conseguir que toda nuestra pieza brillase con un tono gris metálico. Foto 5
Paso 8. Preparación para los taladros.
Con todas las medidas requeridas ya conseguidas, el siguiente paso era taladrar la pieza en 3 partes específicas. Para ello, utilizamos un poco de sulfato de cobre líquido que más tarde aplicamos a la pieza con la ayuda de un trapo. Tras hacer esto, la cara opuesta del alma a las alas tomó un color cobrizo.
Tras preparar la cara del alma solo nos faltaba poder medir y trazar los puntos exactos para los taladros a realizar. Esto lo hicimos con la ayuda de un gramil.
Trazamos líneas rectas en la mitad de la cara, consiguiendo así 4 partes iguales. Posteriormente volvimos a dividir cada uno de esas partes en otras 4. Para finalizar, con la ayuda de una regla y un lápiz trazamos una línea que unía 2 vértices opuestos de esa cara. Foto 6
Paso 9. Marcado de los puntos donde taladrar.
Con la superficie de la cara ya divida en partes iguales, ya sabíamos dónde poder taladrar. Serían 3 agujeros situados en el centro de la misma y 2 más en la intersección de la línea que unía los vértices con la línea de ¼ de la medida longitudinal de la pieza. Foto 7
Con la ayuda de un granete y un martillo marcamos los 3 puntos para facilitar que la broca del taladro no se moviera mucho al realizar su trabajo.
Paso 10. Colocación de la pieza en el taladro.
Colocamos la pieza horizontal en la máquina y la fijamos mediante un gato para intentar que no se desplazara al realizarles los taladros. Foto 8
Paso 11. Elección de las brocas para taladrar.
Como los agujeros a realizar tenían que tener unas medidas exactas de 10 milímetros para el central y de 8,5 milímetros para los externos, tuvimos que elegir unas brocas de métrica especifica. Foto 9
Para realizar los taladros lo haríamos en 2 fases, primero usaríamos una broca más pequeña y luego terminaríamos con la definitiva. Por lo tanto, utilizamos 3 brocas diferentes:
-
Métrica 6,75 para el agujero inicial del centro
-
Métrica 8,50 para el agujero final del centro
-
Métrica 5,50 para los agujeros iniciales externos
-
Métrica 6,75 para los agujeros finales externos
Paso 12. Realización de taladros.
Con la pieza bien fijada y las brocas elegidas, procedimos a realizar los taladros teniendo mucho cuidado de realizarlos en el punto exacto, cosa muy complicada puesto que las brocas se movían muchísimo al taladrar. Foto 10
Paso 13. Realización de las roscas.
Para la realización de las roscas interiores en los taladros utilizamos 1 terraja. Como los diámetros de los agujeros son diferentes tuvimos que utilizar machos de terraja de diferente calibre. Para los dos exteriores utilizamos el calibre 8 y para el central el calibre 10. Estos machos vienen en pequeños sets de 3 unidades, introduciéndose primero el de menor “dentado”. Foto 11
Paso 14. Finalización de la práctica.
Con todo esto, la pieza ya tiene las medidas exactas pedidas para finalizar la práctica así como los taladros roscados. Vistas finales. Isometria final
5. Croquis de la pieza acotada en estado inicial y final
6. Pedido de materiales y herramientas
Para la realización de la práctica hemos utilizado los siguientes materiales y herramientas:
-
Pieza UPN 80
-
Banco o mesa de trabajo
-
Tornillo de sujeción
-
Limas planas
-
Limas triangulares
-
Cepillo de pues de acero
-
Escuadras de acero
-
Calibre o pie de rey
-
Gramil
-
Sulfato de cobre y trapo
-
Regla y lápiz
-
Granete y martillo
-
Taladro y brocas
-
Gato de sujeción
-
Terraja y machos de diferentes medidas
-
Cepillo y recogedor de limpieza
7. Seguridad e higiene
Tanto el profesor Flores como la profesora María José nos hicieron muchísimo hincapié en la necesidad de llevar la ropa adecuada para trabajar en el taller, así como los EPIS (equipos de protección individual) necesarios para la realización de la práctica. Aparte de esto, había que tener en cuenta los riesgos asociados al trabajo a realizar.
Riesgos asociados existentes:
-
Caída de persona a mismo nivel
-
Caída de herramienta o material a distinto nivel
-
Choques con objetos en manipulación
-
Atrapamientos
-
Pisada de objetos en el suelo
-
Contactos eléctricos
-
Cortes superficiales en la piel
-
Proyección de partículas
-
Aspiración de partículas
-
Choques contra objetos inmóviles
-
Sobreesfuerzos y malas posturas
Para evitar estos riesgos tuvimos que tomar una serie de medidas colectivas:
-
Las maquinas a utilizar debían tener el marcado CE correspondiente.
-
Mantener el espacio de trabajo limpio y ordenado.
-
El banco o mesa de trabajo debía de estar calzada correctamente.
-
Evitar objetos y cables en el suelo.
-
Herramientas en buen estado.
-
Utilización de las herramientas según lo aprendido
-
Tener una buena ergonomía en el trabajo
-
Descansos físicos cada 1 hora
-
Formación e información sobre las herramientas a utilizar
-
Utilización de EPIS
Los EPIS asociados y utilizados para la realización de la práctica fueron los siguientes:
-
Guantes
-
Botas de seguridad
-
Gafas de protección
-
Ropa de trabajo
8. Bibliografía
Físicos
Apuntes de clase de la profesora María José
Videos vistos en clase
Información dada por los profesores de la asignatura en el taller
Internet
http://www.construmatica.com/construpedia/Acero
https://es.wikipedia.org/wiki/Acero_aleado
http://ingemecanica.com/tutorialsemanal/tutorialn101.html
http://www.utp.edu.co/~publio17/ac_aleados.htm
http://www.edu.xunta.es/centros/iescamposanalberto/aulavirtual/file.php/117/Tema2_Oxidacion.pdf
https://iesvillalbahervastecnologia.files.wordpress.com/2010/09/oxidacion-y-corrosion.pdf
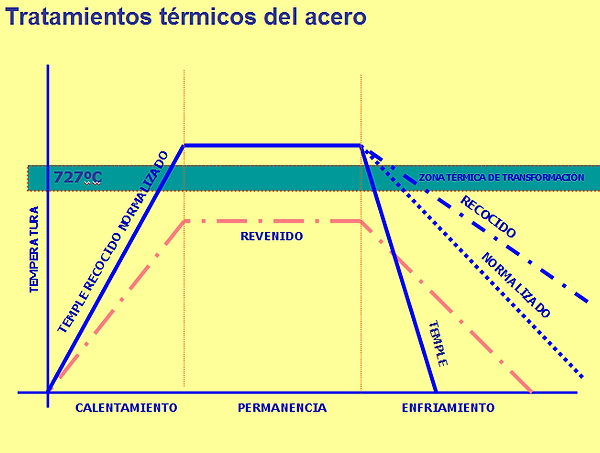
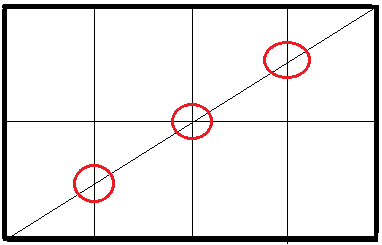